Eddy current inspection is one of several NDT methods that use the principal of electromagnetism as the basis for conducting examinations.”
One of the major advantages of eddy current as an NDT tool is the variety of inspections and measurements that can be performed. In the proper circumstances, eddy currents can be used for:
- Crack detection
- Material thickness measurements
- Coating thickness measurements
- Conductivity measurements for:
- Material identification
- Heat damage detection
- Case depth determination
- Heat treatment monitoring
Crack detection
- Eddy current crack detection equipment can be divided into high frequency instruments for finding surface breaking cracks in ferrous and non-ferrous materials and low frequency instruments for finding cracks in non-ferrous materials.
- Detection of subsurface cracks in ferrous materials is possible but only when they have been saturated magnetically to remove permeability effects. This is complex and is only practicable in automated tube testing systems. Eddy current tests are the most sensitive of all NDT methods to surface cracks. High frequencies of the order of 2MHz give high resolution, but the probes are small and covering large surface areas takes a long time.
- Low frequency crack detectors need larger probes to allow for suitable coil inductances. The frequency setting is critical and is in the range 100Hz to l00kHz depending on the depth of penetration required. Subsurface eddy current fields are influenced more by phase changes than amplitude changes and therefore phase sensing circuits are essential.
- Although traditionally they were meter reading instruments, the trend in crack detectors is towards instruments with cathode ray tube displays for their added versatility.
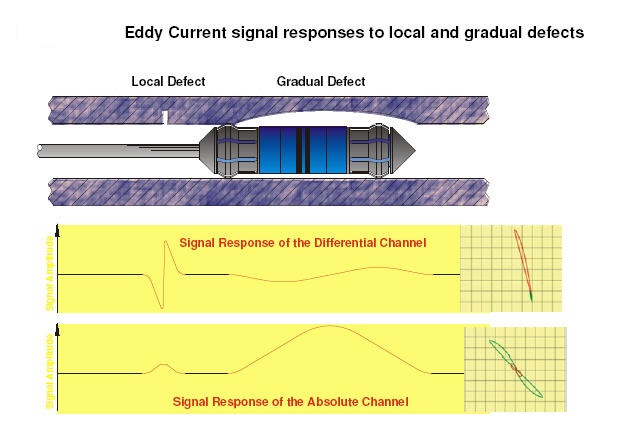
Tube and wire testing
- Automated eddy current test systems have been developed for inspecting tube, bar and wire at speeds up to 3 m/s.
- Once the operator has calibrated the instrument using a tube or wire with known flaws, the test installation runs automatically, ejecting defective pieces from the production line or marking them with paint.
- The mechanical handling equipment for the test pieces becomes so complex that the actual eddy current test instrumentation may appear an insignificant part. Facilities for magnetic saturation and demagnetisation of ferrous tubes and wires, increase the capital costs considerably.
- The constant test speeds and differential coils allow for modulation of the test signals with the speed and then filtering to remove noise. Unfortunately, when using differential coils, it is possible to pass tubes (which contain consistent defects over their entire length) through the eddy current system, without detection. Because of edge effects, tube ends cannot be detected. Extrusion defects along the centre of bars cannot be detected either because the eddy current field from an encircling coil is at zero intensity at the centre of a solid cylinder.
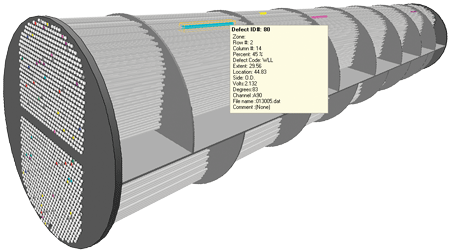
Condenser tube inspection
- This application is currently receiving a great deal of attention in connection with the heat exchangers of pressurised water reactors.
- Tube thinning is the main defect and by selecting what is known as the f90 frequency, signals resulting from thinning on the outside surface can be set 90° out of phase from signals arising from thinning on the inside surface. By recording the X and Y signals from the impedance diagram on a two-channel strip chart recorder, the extent of thinning can be ascertained at test speeds of 200-300mm per second.
- A major problem is caused by the baffle plates which separate the condenser tubes. The tubes are non-magnetic, stainless steel, cupro-nickel or more recently, titanium. The baffle plates are ferrous and the permeability signal is enough to obliterate signals from thinning between the tube and baffle plate. To alleviate this problem, instruments have been developed to operate with two frequencies simultaneously. The separate signal phases are then mixed in a manner which removes unwanted permeability effects.
- Inspection is usually done with differential coils because they do not drift with temperature changes. The signal interpretation is more difficult and it is often necessary to do supplementary tests with absolute coils.
- Other recent developments include use of computers to analyse the X and Y channels for defect signals. Inspection can then be done in real time
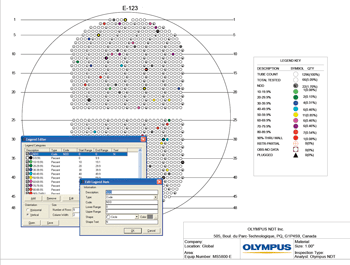
Material sorting
- Ferrous segregators and electromagnetic sorting bridges are useful tools in sorting steels which have been hardened.
- Conductivity meters can be used to sort aluminium and copper alloys, both for compositional variations and hardness variations.
- Great care has to be taken to ensure that the variation being detected is the relevant one. For example, the change in the conductivity of an aluminium alloy may be due to a change in composition or a change in its hardness. Because eddy current fields penetrate below the surface of the test material, the method provides a better sample of material properties than many other material sorting methods and more importantly it is very rapid.
Weld testing
- Simple high frequency eddy current testers have been used for some time to detect toe cracks in ferrous welds. The method has the advantage of being able to detect cracks through paint layers. The disadvantages lie in the high noise levels caused by permeability changes in the weld and lift-off noise from rough cap surfaces.
- Recent devices have to some extent overcome these problems. They are being used to supplement magnetic particle inspections underwater, to distinguish strong spurious indications from toe cracks. The equipment uses a cathode ray tube with a vector point display and special coil arrangements.
Coating thickness measurement
- The high near surface resolution of eddy current testing makes it useful for measuring coatings, both metallic and paint, on metal substrates.
Some of the advantages of eddy current inspection include:
- Sensitive to small cracks and other defects
- Detects surface and near surface defects
- Inspection gives immediate results
- Equipment is very portable
- Method can be used for much more than flaw detection
- Minimum part preparation is required
- Test probe does not need to contact the part
- Inspects complex shapes and sizes of conductive materials
Some of the limitations of eddy current inspection include:
- Only conductive materials can be inspected
- Surface must be accessible to the probe
- Skill and training required is more extensive than other techniques
- Surface finish and and roughness may interfere
- Reference standards needed for setup
- Depth of penetration is limited
- Flaws such as delamination that lie parallel to the probe coil winding and probe scan direction are undetectable.